Hey everyone, just wanted to share a simple way I use to sand out imperfections inside tubing, sometimes I find I burn through thin seat tube tubing while welding and end up with a spot inside the tube that will not allow the seat post to fit properly. Or there is rust inside a fork tube that will not let the stem fit properly.
Normally you can just fix it with a half-round or rattail file, but sometimes you need to smooth even further, or deeper than a file can reach, that is where this method works well.
Start with a piece of 3/8 rod and cut a slot in the end:
Slide a piece of doubled over sand paper strip into the slot you created:
Hammer the slot down closed on the sandpaper so it is held in a bit better:
Roll the sandpaper around the rod in the direction your drill travels:
Fit the other end of the rod into your drill and the sandpaper end into the tube and ream away with an up and down motion similar to honing the bores on an engine block.
Keep checking your sandpaper is remaining firmly held in the slot, as you don't want to lose it inside the tube. Pretty soon you will have a tube that works as intended:
Luke.
UPDATE April 2019:
The above method is very good for small amounts of reaming, but sometimes the tube shrinks a fair amount when welding and you need something more aggressive...
A 26mm (for a 1" tube) mill broach welded to an old bolt works well, just make sure you use some sort of cutting fluid/lubricant (I use ATF) and hold on!
Normally you can just fix it with a half-round or rattail file, but sometimes you need to smooth even further, or deeper than a file can reach, that is where this method works well.
Start with a piece of 3/8 rod and cut a slot in the end:
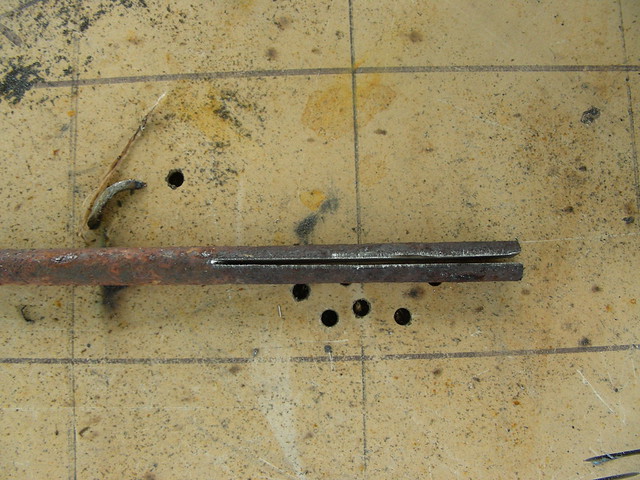
Slide a piece of doubled over sand paper strip into the slot you created:
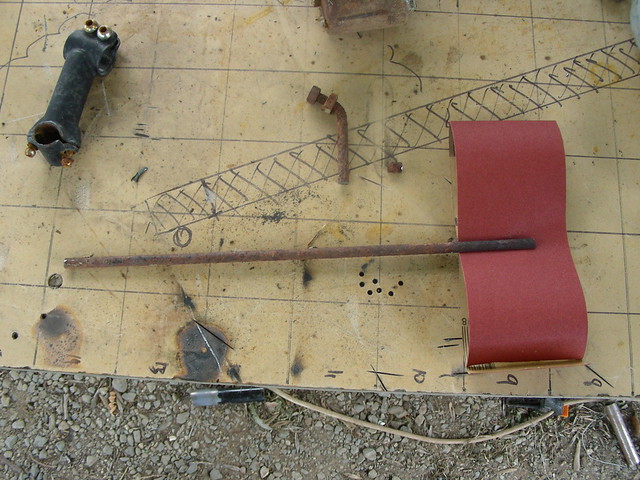
Hammer the slot down closed on the sandpaper so it is held in a bit better:
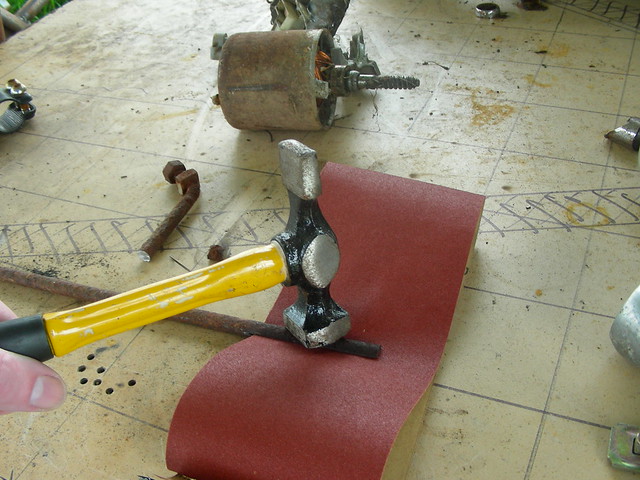
Roll the sandpaper around the rod in the direction your drill travels:
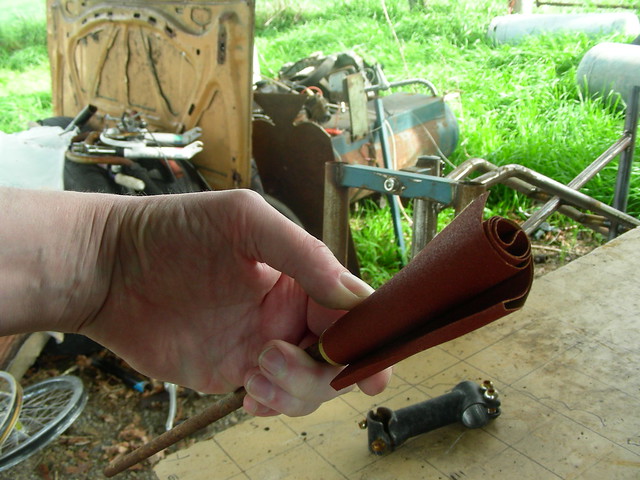
Fit the other end of the rod into your drill and the sandpaper end into the tube and ream away with an up and down motion similar to honing the bores on an engine block.
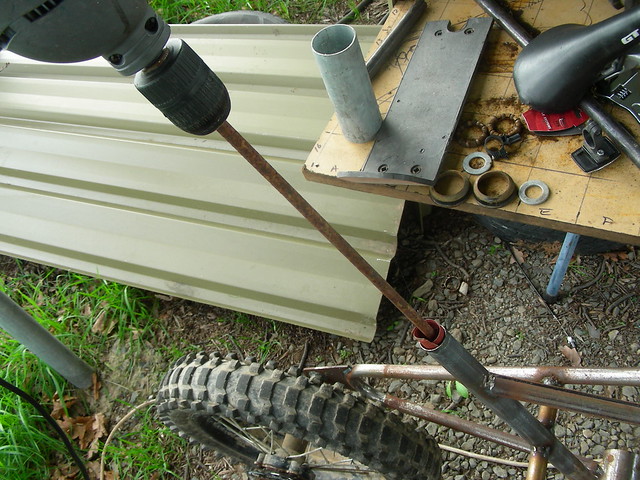
Keep checking your sandpaper is remaining firmly held in the slot, as you don't want to lose it inside the tube. Pretty soon you will have a tube that works as intended:
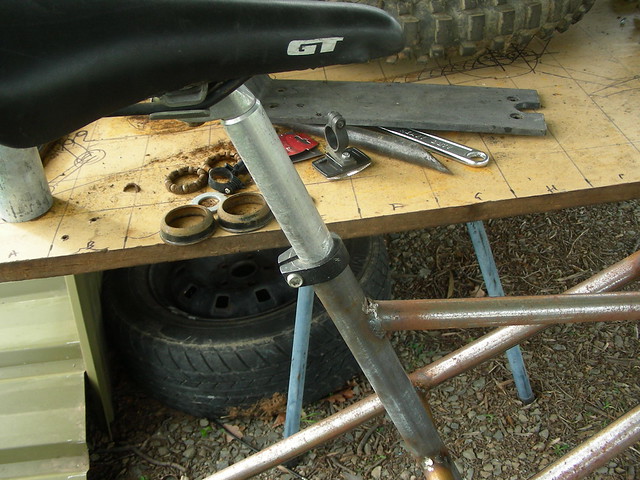
Luke.
UPDATE April 2019:
The above method is very good for small amounts of reaming, but sometimes the tube shrinks a fair amount when welding and you need something more aggressive...
A 26mm (for a 1" tube) mill broach welded to an old bolt works well, just make sure you use some sort of cutting fluid/lubricant (I use ATF) and hold on!

Last edited: