I think everyone agrees that Monark springer forks look great. The originals are rare and expensive. I think everyone would also agree that the new reproduction Monark forks are somewhat underbuilt and lacking in quality control. I looked into the problems and figured out how to properly fix them, making the new Monark fork a safer and stronger option. I use them on motor bikes that cruise at over 30 mph, so I could not accept anything less than completely reliable springer forks. By disassembling a few sets I found consistant problems. The forks are not fully welded and the steer tube does not have a flared area to press on a crown race. If you can't press this race into place you will always have movement under braking and when hitting bumps. Here is what I found under the polished fork crown cover.
What you'll notice is the two fork blades enter into the three crown plates from below, and the steer tube enters into these plates from above. Notice the complete lack of welding through this area. The fork blades were only welded to the bottom plate so the forks could tear lose from the upper plate and cause a complete failure. Also, the steer tube was only welded to the bottom plate and all three crown plates were only tacked welded together. So, how to fix them? Basically four things need to happen.
1. Weld the fork tubes to the upper crown plates, effectively joining the upper and lower crown plates and removing the ability of the tubes from tearing loose of the upper crown plates.
2. Weld all three crown plates together wherever they meet so that no flexing can occur between these plates.
3. Weld the steer tube all the way around where it passes through the upper crown plate, removing any flexing or movement in this area.
4. Place the properly welded fork into a lathe by the steer tube and then turn down the steer tube weld within .020" of the steer tube diameter, giving a press fit for a crown race.
Here is a picture of the fully tig welded fork before machining.
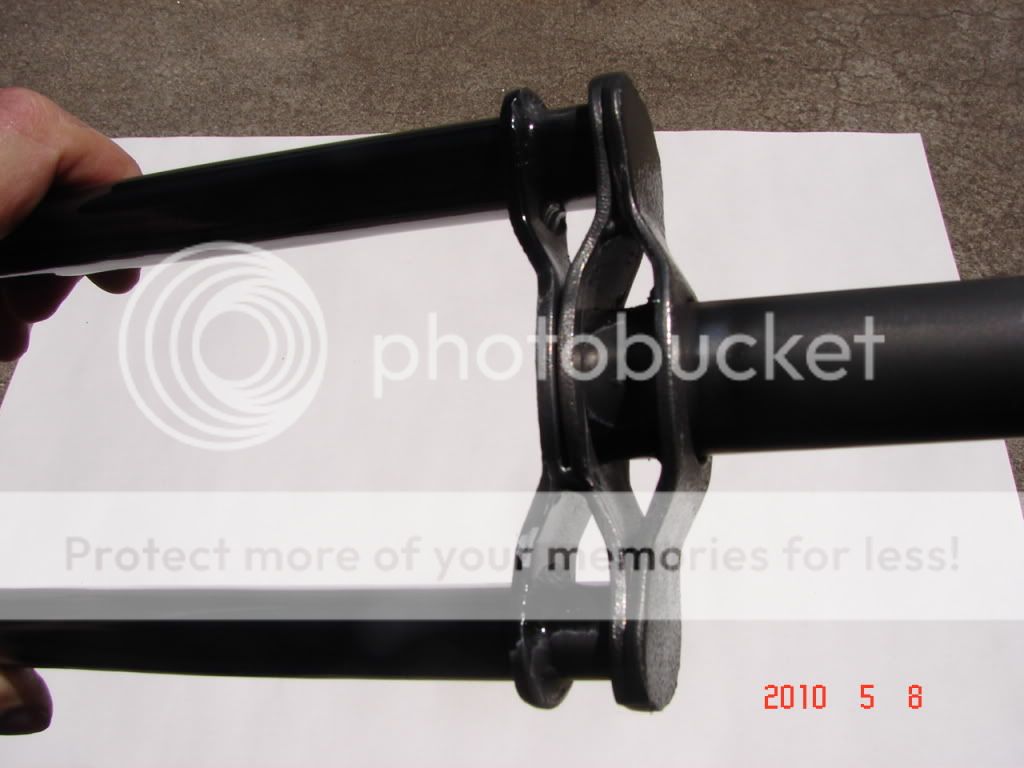
What you'll notice is the two fork blades enter into the three crown plates from below, and the steer tube enters into these plates from above. Notice the complete lack of welding through this area. The fork blades were only welded to the bottom plate so the forks could tear lose from the upper plate and cause a complete failure. Also, the steer tube was only welded to the bottom plate and all three crown plates were only tacked welded together. So, how to fix them? Basically four things need to happen.
1. Weld the fork tubes to the upper crown plates, effectively joining the upper and lower crown plates and removing the ability of the tubes from tearing loose of the upper crown plates.
2. Weld all three crown plates together wherever they meet so that no flexing can occur between these plates.
3. Weld the steer tube all the way around where it passes through the upper crown plate, removing any flexing or movement in this area.
4. Place the properly welded fork into a lathe by the steer tube and then turn down the steer tube weld within .020" of the steer tube diameter, giving a press fit for a crown race.
Here is a picture of the fully tig welded fork before machining.
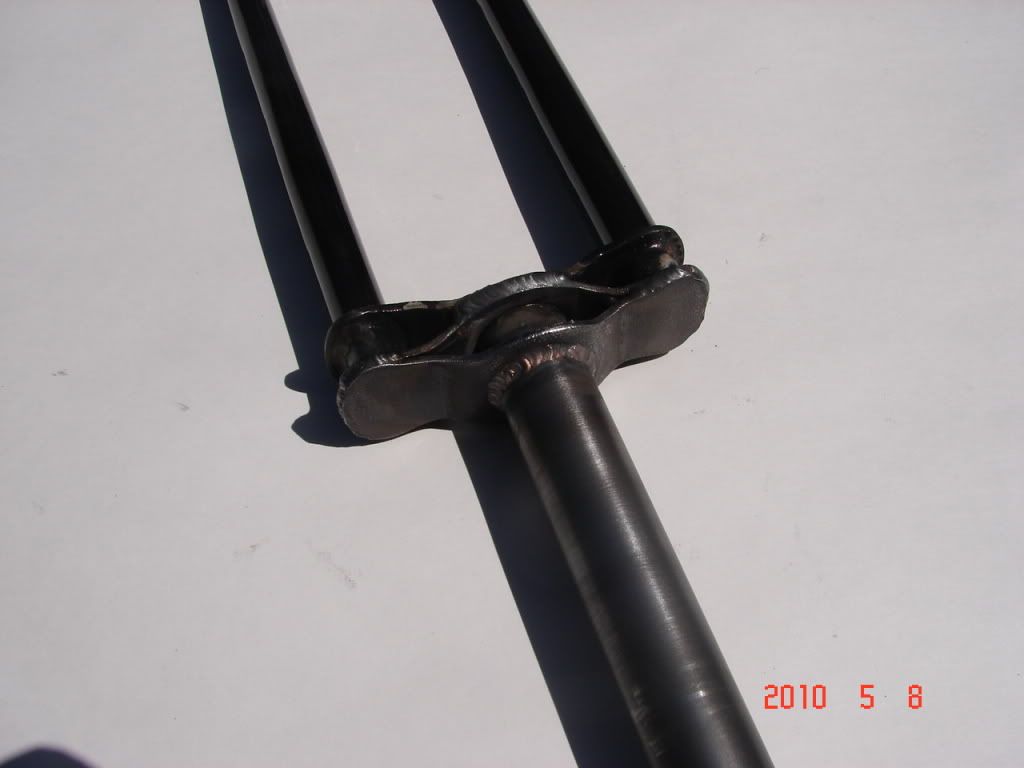