Been meaning to do this for a while, but to be honest I was a bit scared of it, last thing I wanted was to destroy a good rim by not tensioning it right or just plain fail at getting the lacing pattern right.
My health has been a bit off again lately so I have not been outside welding and grinding, but there is only so long you can sit inside looking at a computer without losing the remains of your sanity, so I decided I needed something to do, something not too physical and it would be good if it was productive, so I decided to give it a go!
I needed a particular hub and rim combination for a future build that is rather hard to find pre-made so it was a perfect excuse to build one up out of parts I have lying around, measured the spoke hole diameter of the hub, found a wheel the right size with a similar size spoke hole diameter and stripped it for the spokes, it donated 48 so I was able to pick and choose the best 32 for this build, the nipples were a bit chewed up so I grabbed the ones off the rim I pulled the hub from to use instead as they were nicer anyway and set to work, took my time and triple checked everything as I went so it took me 1.5 hours all up including truing the wheel at the end but I am happy with that, it was all pretty simple and logical, it was time consuming and fiddly at times, but is something I will definitely do again!
I was surprised by how easy it is to true the wheel once you get the hang of it, amazing how even half a turn can make such a difference! I got it close and was going to leave it there thinking it was good enough, but decided to just tweak it a little more and got it really straight within another 5 minutes, really happy and now I am wondering why I waited so long!
So here it is, a downhill mountain bike disc brake offset hub mounted to a heavy duty 20x1.75 aluminium rim, with a 203mm disc brake rotor for good measure:
I would have preferred if it was not a quick release hub as I have heard horror stories with disc brakes and quick releases coming lose but I will fix that when I build the bike by mounting the calliper in front of the fork instead of behind, so when the brakes are applied the wheel tries to move further into the dropouts rather than down and out of them.
Best bit of the whole thing? Aside from the 15 minutes spent truing the wheel, I did the whole lot sitting in a comfortable chair in our air-conditioned dining room!
If you have been wanting to do it, but have been putting it off, really, just give it a go!
Luke.
My health has been a bit off again lately so I have not been outside welding and grinding, but there is only so long you can sit inside looking at a computer without losing the remains of your sanity, so I decided I needed something to do, something not too physical and it would be good if it was productive, so I decided to give it a go!
I needed a particular hub and rim combination for a future build that is rather hard to find pre-made so it was a perfect excuse to build one up out of parts I have lying around, measured the spoke hole diameter of the hub, found a wheel the right size with a similar size spoke hole diameter and stripped it for the spokes, it donated 48 so I was able to pick and choose the best 32 for this build, the nipples were a bit chewed up so I grabbed the ones off the rim I pulled the hub from to use instead as they were nicer anyway and set to work, took my time and triple checked everything as I went so it took me 1.5 hours all up including truing the wheel at the end but I am happy with that, it was all pretty simple and logical, it was time consuming and fiddly at times, but is something I will definitely do again!
I was surprised by how easy it is to true the wheel once you get the hang of it, amazing how even half a turn can make such a difference! I got it close and was going to leave it there thinking it was good enough, but decided to just tweak it a little more and got it really straight within another 5 minutes, really happy and now I am wondering why I waited so long!
So here it is, a downhill mountain bike disc brake offset hub mounted to a heavy duty 20x1.75 aluminium rim, with a 203mm disc brake rotor for good measure:
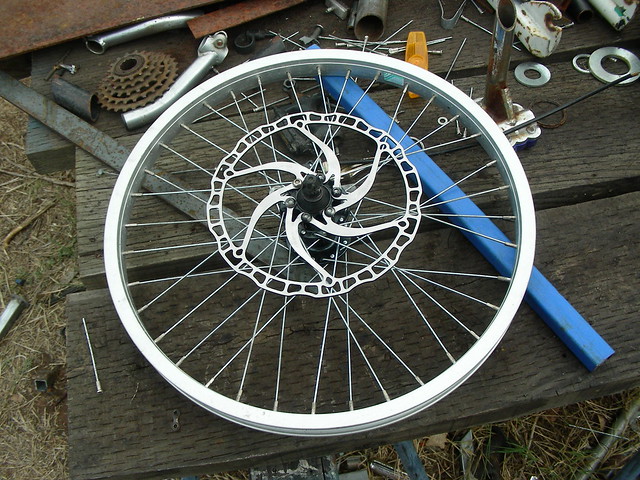
I would have preferred if it was not a quick release hub as I have heard horror stories with disc brakes and quick releases coming lose but I will fix that when I build the bike by mounting the calliper in front of the fork instead of behind, so when the brakes are applied the wheel tries to move further into the dropouts rather than down and out of them.
Best bit of the whole thing? Aside from the 15 minutes spent truing the wheel, I did the whole lot sitting in a comfortable chair in our air-conditioned dining room!
If you have been wanting to do it, but have been putting it off, really, just give it a go!

Luke.