I came up with a way to run a modern rear V-brake (rim brake) on a vintage frame. My goal was to make it a modular bolt on set up without welding posts on the vintage frame. Anyhow, I tested them out last night and they work great. Pretty simple set up. I bought a 14mm split shaft collar (.551") and TIG welded a 10mm X 1.25 nut to it. On the side of the 10mm nut I TIG welded a .125" X .375" dia roll pin to be used as a clocking feature for the V-brake return spring. The 14mm split shaft collar matched the diameter of my 63 Schwinn frame tubing. However, any split shaft collar size could be substituted, standard or metric, to fit just about any frame. Check it out.
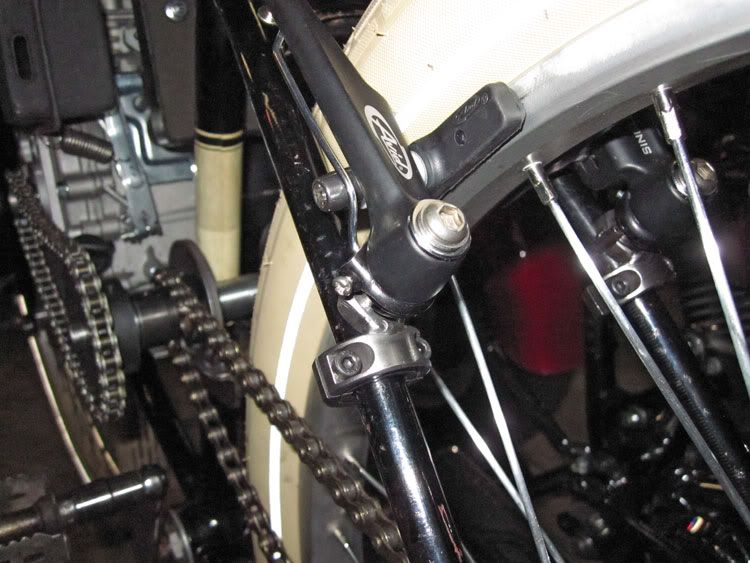
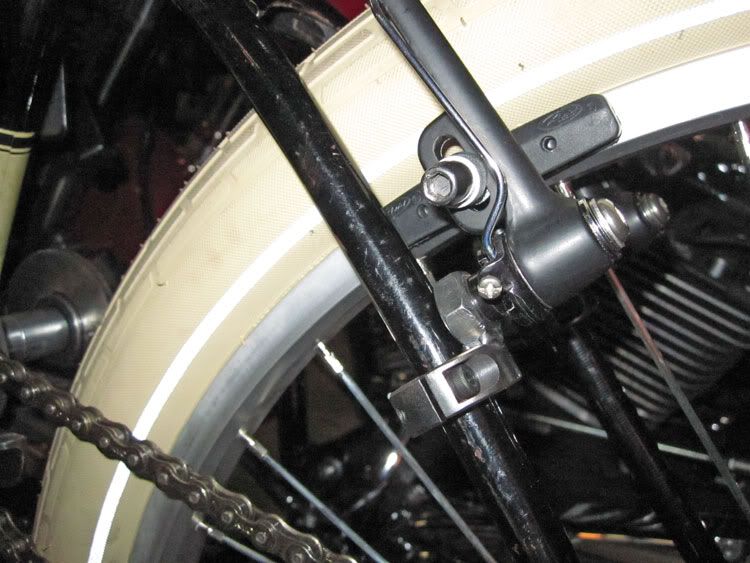
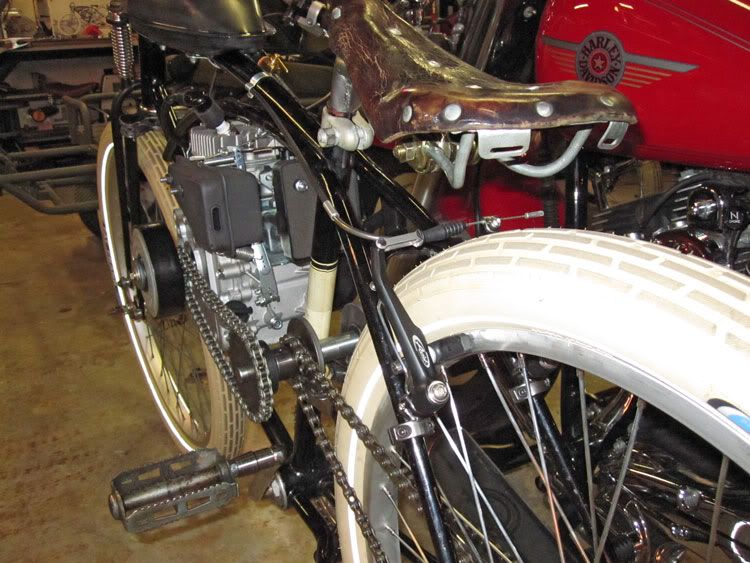